Testing Materials
To decide which material would be best suited for a dog-waste bag, I tested the materials on seven factors: thickness, heat resistance, ability to weld with self, ability to hold weight, plasticity, ability to repel water, and sustainability. I also did these tests on a zip-lock plastic bag as a control. The ideal outcome for an adequate material would be: below .1 mm of thickness, moderate resistance to heat, can weld with self when heated, can hold at least 500 grams of weight, can be bent without ripping, can repel water, and is biodegradable/sustainable. I scored 6 factors out of 10 (10 being the most desirable and 1 being the least desirable.) I scored 1 factor (sustainability) out of 25 because that factor holds the most significant relevance to this project.
After testing materials 1, 2, and 3, I determined which materials showed the most promise. I determined that material 3 showed the most potential but needed to be more flexible and hydrophobic. I developed material 3.2 by including silicon oil, more vegetable glycerin, and more sorbitol to improve both the ability to repel water and the ability to bend. I then ran all tests with material 3.2 and recorded the results.
Variable | Material 1 | Material 2 | Material 3 | Material 3-2 | Control |
---|---|---|---|---|---|
Total Score | 44/75 | 54/75 | 55/75 | 58/75 | 49/75 |
Downsides | cannot repel water, rips easily, no resistance to heat, can hold very little weight | Slightly too thick, cannot repel water, rips when crinkled | Too brittle, does not repel water | Includes silicon oil, which is not sustainable, low heat resistance | Little heat resistance, very unsustainable (this negative outweighs the positives) |
Upsides | Thickness is ideal, very sustainable, | Very sustainable, melds to self, can hold a lot of weight (more than needed), high heat resistance | Very sustainable, slightly melds to self, can hold a lot of weight, some heat resistance | Able to repel water, melds to self, does not rip when crinkled, able to bear weight | Can repel water, good thickness, good plasticity |
Sustainability | All biodegradable ingredients with renewable sources and can be harvested sustainably
Score: 25/25 | All biodegradable ingredients with renewable sources and can be harvested sustainably
Score: 25/25 | All biodegradable ingredients with renewable sources and can be harvested sustainably
Score: 25/25 | Silicon oil is not biodegradable or sustainable
Score: 15/25 | Single-use plastic is very unsustainable and not biodegradable
Score: 0/25 |
Ability to hold weight | Max weight: clamp + 500 g Score: 3/10 | Max weight:
clamp + 1.9 kg
Score: 9/10 | Max weight:
clamp + 2 kg
Score 10/10 | Max weight:
Clamp + 700 g
Score: 8/10 | Max weight:
Surpassed test, can hold up to 15 lb
Score: 10/10 |
Ability to repel water | When in contact with water the material became thinner and did not repel water,
Became more hydrophobic after exposed to heat
Score: 3/10 | When in contact with water became thinner and soaked in the water
Score: 2/10 | When in contact with water became thinner and did not repel water
Score: 3/10 | Able to repel water before and after heat
Score: 10/10 | Able to repel water before and after heat
Score: 10/10 |
Plasticity | Rips when crinkled and bent
Score: 1/10 | Rips when crinkled and bent
Score: 1/10 | Rips when crinkled and bent
Score: 1/10 | Does not rip when crinkled, great consistency and stretch ability
Score: 8/10 | Does not rip when crinkled, very flexible
Score: 10/10 |
Ability to weld with self | Will not meld with itself
Score: 1/10 | Slightly welds to self but not strongly
Score: 4/10 | Slightly melds to self
Score: 6/10
| Melds to self seamlessly, strong
Score: 10/10 | Melds to self seamlessly, strong
Score: 10/10 |
Heat Resistance | Burned almost straight away, little to no heat resistance
Score: 3/10
| High heat resistance, turns brown quickly and shrivels up when exposed to heat, melts least quickly out of all materials
Score: 8/10 | Some heat resistance, eventually melted to hot plate
Score: 5/10 | Some heat resistance, melts when in contact with heat very similarly to control
Score: 3/10 | Very little heat resistance, melts right away
Score: 1/10 |
Thickness | 0.08 mm Score: 8/10 | 0.12 mm Score: 5/10 | 0.13 mm Score: 5/10 | 0.14 mm Score: 4/10 | 0.04 mm Score 8/10 |
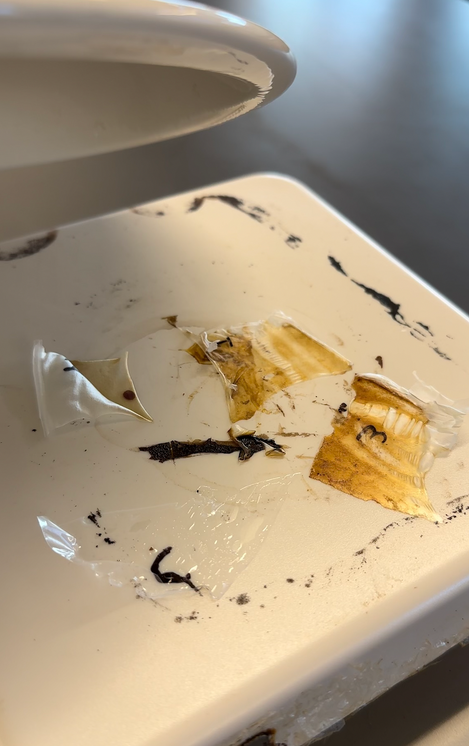
Conclusion & Further Research
Due to time restrictions, the last iteration of material was material 3.2. However, given more time, I would have continued this process to create an even more ideal material. Based on the various tests and scoring material, 2, 3, and 3.2 were the most ideal, scoring 54, 55, and 58, respectively. As seen in the chart, each material has its upsides and downsides, so it would not be satisfactory to choose only one best material. I have concluded that if I were to continue experiments, I would iterate further off of material 3 and material 2. Material 3.2 was my attempt to iterate off of material 3; however, it was not very sustainable due to the use of silicon oil. Sustainability was the primary goal of this project and is most important in the materials I created. Based on this perimeter alone, materials 1,2, and 3 score highly and indicate good candidates to modify further.
In terms of further research, I want to find a way to modify material 3 (not 1 due to its lack of strength and not 2 due to its inability to weld to itself) to create greater plasticity and ability to repel water sustainably. In industry, some materials are processed a certain way to repel water. In a future experiment I would like to experiment with different methods of drying and processing the material after I create it. In these experiments, I only used the method of drying it with parchment paper. In my research, I read about the use of hydrophobic coatings applied after a material is made to make it repel water. If I had more time, I would try to experiment with various sustainable hydrophobic coatings, such as a natural wax-based coating, to treat my materials.
Furthermore, I propose to adjust the amount of gelatin and sorbitol to increase plasticity. In material 3.2, I used 4 g of sorbitol and 4 mL of glycerin, which proved to be excessive. Conversely, in material 3, I used 2.25 g of sorbitol and 1 mL of glycerin, which was insufficient. Based on these trials, I would aim to use 3 g of sorbitol and 2 mL of glycerin, a balance that I believe would enhance the plasticity of the material.
Overall, this process was a success! I met my goal of creating a sustainable plastic alternative, but there is still a long way to go in terms of optimizing said material.